Climate change is a global and urgent concern, one that demands collaboration and concerted actions across disciplines and countries. In Paris, at the UN Climate Change Conference (COP21), world leaders made a historic breakthrough by agreeing to reduce greenhouse gas emissions, which are the primary cause of global warming. It was enacted on November 4, 2016, after being approved by around 200 nations on December 12, 2015 [1]. It is today just as imperative that we achieve carbon neutrality sometime between 2050 and 2100, by restricting greenhouse gas emissions contributed by humans to levels that trees, soil, and oceans can recover naturally from (known as net zero). Reforming the present industrial processes in order to lower greenhouse gas emissions and encouraging the collection of from the atmosphere are the most significant challenges, to which scientists are finding an increasing number of solutions [2]. A major contributor of emissions into the atmosphere is the construction industry. The built environment generates 40% of all yearly worldwide CO2 emissions. Building operations (i.e. running buildings during their life time) account for 27% of total carbon emissions each year, while building and infrastructure materials and construction (also known as embodied carbon) account for an additional 13% [3].
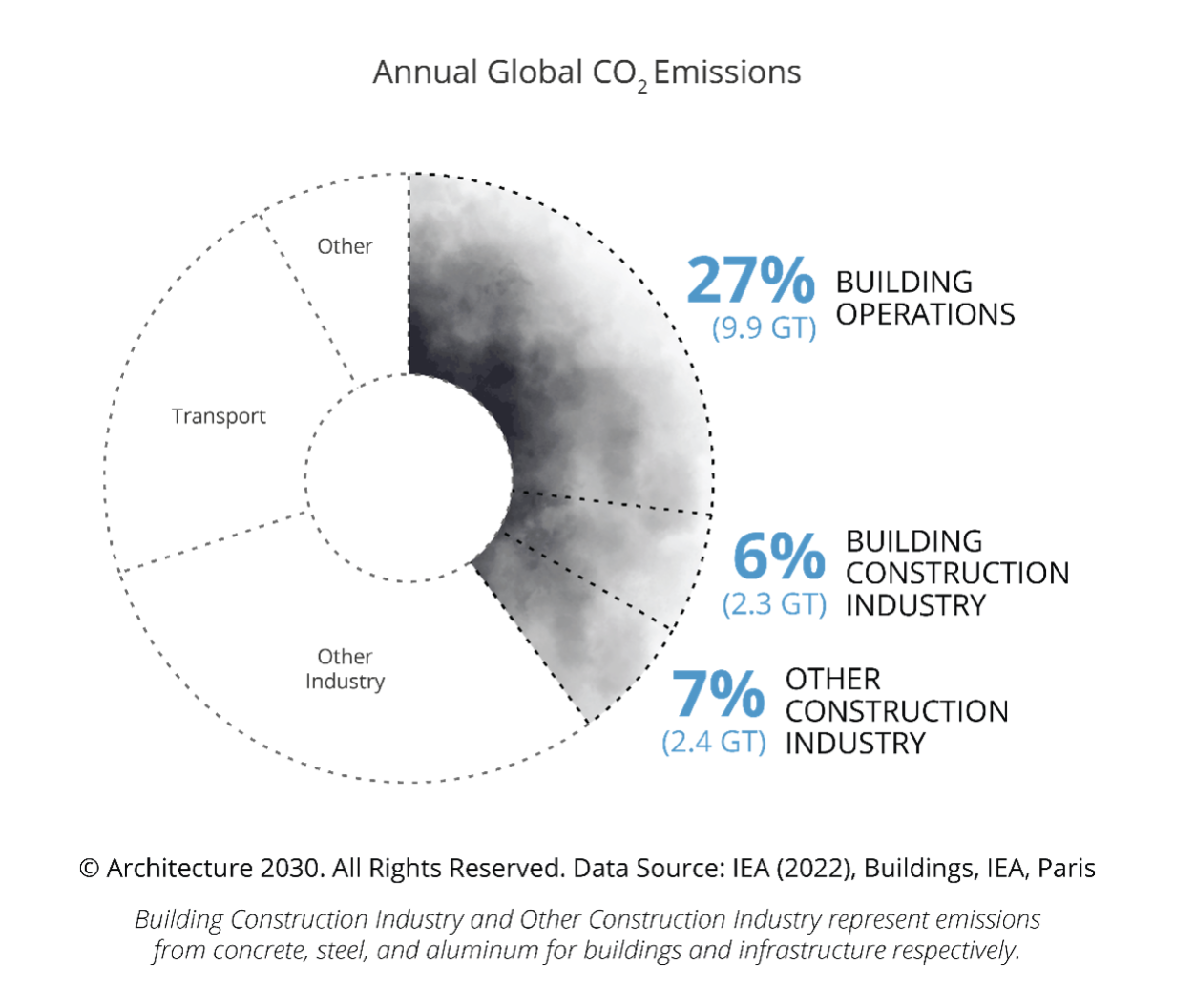
One of the least environmentally friendly sectors of the economy, the construction sector accounts for 40% of world energy consumption, 44% of material use, and 40–50% of greenhouse gas emissions [4]. Reducing carbon emissions is generally acknowledged as an essential requirement to address growing concerns about the effects of global warming. The natural environment has been significantly impacted by the construction industry. There are two major elements to address in our endeavour to mitigate greenhouse gas emissions and in achieving carbon neutrality in construction projects: reducing operational and embodied energy consumption.[5].
The amount of carbon generated during a construction project is known as embodied carbon. Embodied carbon is emitted during the processing of raw materials, manufacturing, refining of goods, distribution, installation, and disposal of obsolete resources. Embodied carbon is embedded into the structure of the building because it was emitted during manufacturing, transport and installation. On the other hand, the quantity of carbon released after a constructed structure is occupied is known as operational carbon. The latter has been for a long time a primary objective of reduction in construction since it is simpler to assess than embodied carbon and more visible to the public.
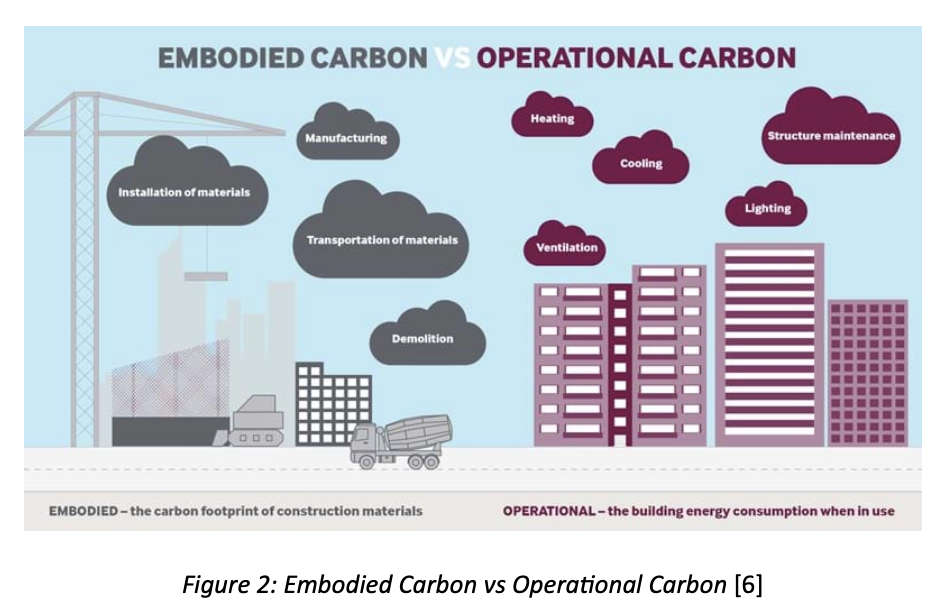
Given that the carbon is released sooner in embodied carbon than during operation, particularly during material processing and structure construction, it has a more immediate impact on the environment. This is referred to as the carbon time value [6]. Consequently, it is essential that structural engineers make every effort to minimise this upfront embodied carbon of the structural system when they design and recommend materials and construction methods.
There are several methodologies for calculating the embodied carbon in structural systems. Each provides insight into the environmental impact. The two most frequent are 1 - To include the overall life cycle of the building, from preliminary extraction of raw materials to the final salvaging of construction materials, or 2 - To only include the effects of some stages, starting with the extraction of raw materials but stopping when the product or structural component is being dispatched from the fabrication facility. In order to 1 - Take into account the complete life cycle implications, a life cycle assessment (LCA) is undertaken, using a specialist software into which one inputs the structural material quantities (SMQ) and allocates material specifications to those measurements. When considering 2 - The product impact only, the embodied carbon is typically measured by dividing the quantities of the structural materials by the embodied carbon factors listed in the environmental product declarations (EPDs) that are publicly available for each material.
There are many solutions and strategies already known and available to the building industry to lower carbon emission. Adoption of more durable materials that can sustain longer use and that are created through a more economical and efficient construction process are key. The use of more durable materials should reduce capital expenses, upkeep, restoration, and maintenance. As opposed to the construction of a new structure, restoration projects often reduce 50 to 75% of the embodied carbon emissions [7], because the majority of the embedded carbon present in the foundation and structure is retained. Concrete is the major contributor of embodied carbon for construction premises, yet low-carbon concrete is simple to create. The building industry should cooperate with structural engineers to consider implementing coal ash, calcined clays, slag, or reduced-strength concrete. Since plastic, aluminium, and foam insulation all possess considerable amounts of carbon footprint, they should be used sparingly or replaced by substitutes. For example, a design structure that uses wood is an attractive substitute to steel and concrete structures. Straw and hemp are also perennially renewable insulating materials. Polished concrete tiles are an excellent substitute for the more polluting carpet or vinyl. Reusing materials such as bricks, metals, timber and even fractured concrete can significantly reduce embodied carbon emissions.
Companies and governments are taking action as it is clear that reducing embodied carbon to the lowest possible level is critical to the net zero carbon target. Every spared carbon emission reduces the need for carbon sequestration which is the process of capturing and storing atmospheric once emitted. Minimising embodied carbon should be a priority for architects and construction firms as embodied carbon limitations become required by law to secure construction development programs and obtain planning permissions. Leading companies are now supporting legislation setting embodied carbon limitations. In the UK, this has resulted in an adjustment to the "Part Z" of the Building Regulations, enforcing evaluation for prior carbon emission limits on all construction projects larger than 1,000 starting in 2027. Furthermore, beginning in 2023, all non-residential projects larger than 1,000 must be evaluated for complete lifecycle carbon emissions and starting in 2025, residential projects must do the same [8]. Similarly, the first Low Emissions Technology Statement (LETS) represents a significant step for the Australian government. The Australian Renewable Energy Agency (ARENA) was established by the Australian government in 2012 to collaborate with the Clean Energy Finance Corporation (CEFC) and other pertinent authorities to achieve net zero carbon emission by favouring low emission generating materials such as low emissions aluminium and steel [9].
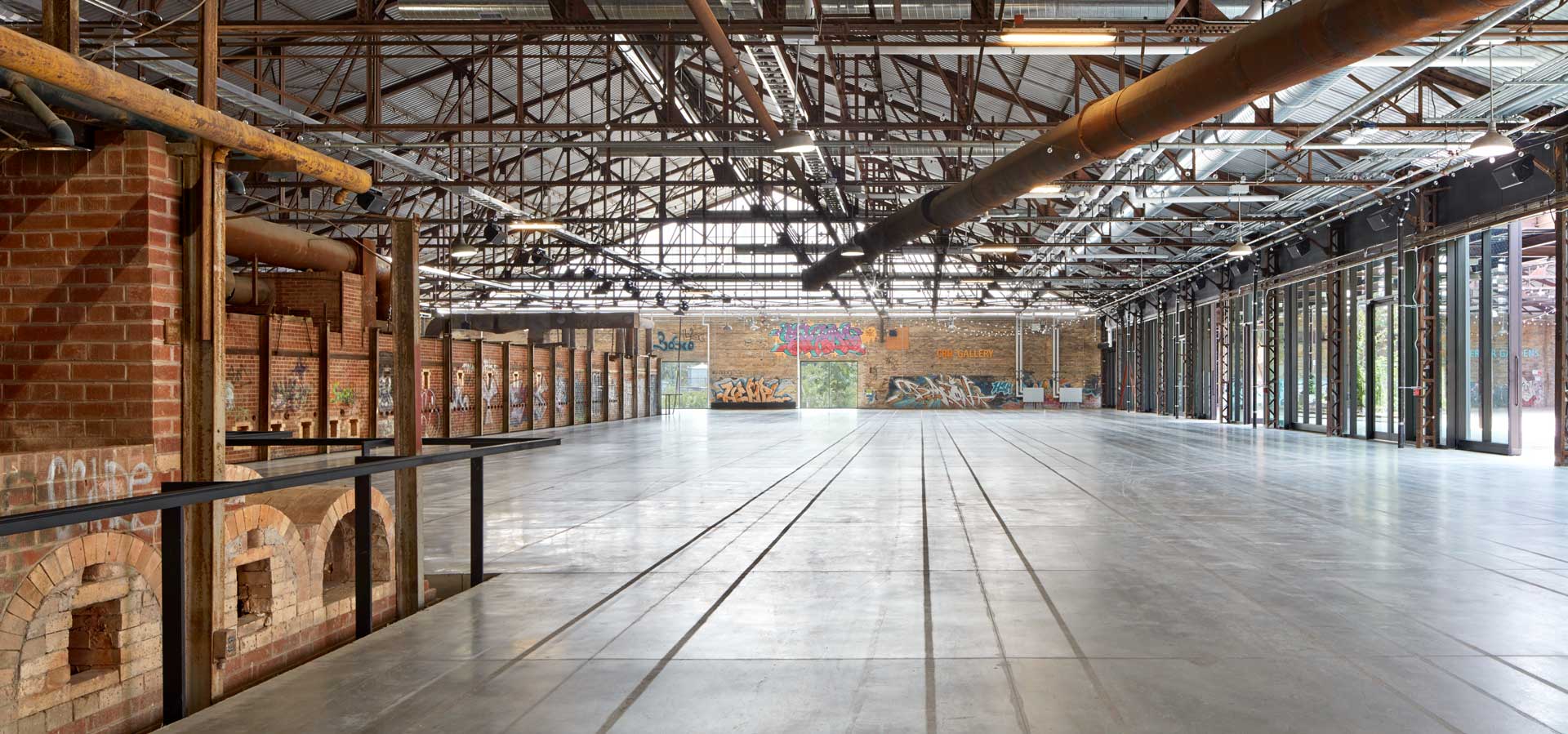
Other recent initiatives include the refurbishment of Don Valley Brick Works’ Kiln Building, now called TD Future Cities Centre in Toronto, as a case study of how to achieve net zero carbon emissions by restoring, i.e. re-using existing materials and structures, selecting lower-carbon materials purchased from local sources, installing renewable energy systems, natural lighting and improved thermal insulation of the building’s envelope, as well as developing a carbon offset strategy. An LCA assessment conducted using a software package called OneClick LCA tool was used to evaluate the embodied emissions related to renovating the existing building. The findings indicated that, under the assumption of a 60-year lifespan, 20% of the carbon produced is attributable to material substitution during the service life of the building, 69% by the materials from extraction to processing during the construction phase, and the majority of the remaining 11% is generated by on-site construction processes and waste disposal. In restoration project such as this, the renewable energy systems and concrete flooring are the primary sources of embodied carbon in building elements. In this case study it is 31% and 26% respectively. But the embodied carbon added to the building through the restoration project is forecast to be balanced by savings in operational energy related to heating, cooling and lighting, within 3–13 years, [10].
A case study has been conducted in Sweden to determine the net gain from retrofitting an existing house to turn it into a passive house, i.e. one much more energy efficient to run. Specifically, it tried to calculate whether the emissions during the retrofit outweigh the future savings related to the operation of the building. The operation energy savings that could be achieved were calculated to be between 50% and 82% depending on the passive house standard used. And the construction cost of the retrofit could be substantially reduced by careful selection of construction materials, for example wood for building frames can lead to a 68% decrease. So all things considered, the embodied carbon of the retrofit was deemed to be between 4% and 25% of the operation emissions over the life time of the house, making the retrofit significantly beneficial [11]. LCA studies are also being conducted to compare materials. This was done in continental Mediterranean regarding insulation materials and concluded that, while all insulating materials provide a net positive effect considering 55 year’s lifespans, the largest environmental impact is linked to the polystyrene insulation material and the least with the mineral wool [12].
The importance and urgency of the issue call for concerted efforts between the scientists who lead the research into new materials and energy saving solutions, the architects and civil engineers who prescribe possible materials and methods of construction, businesses who choose amongst those materials and methods based on commercial factors, and governments who should give incentives to all those parties or even pass laws that make some of those materials and methods mandatory. The key to our future lies in a successful collaboration of all those stakeholders.
References
[1] Helen Briggs, “Why is the Paris climate agreement important for COP26? - BBC News,” Oct. 25, 2021. https://www.bbc.com/news/science-environment-35073297 (accessed Sep. 25, 2022).
[2] F. Wang et al., “Technologies and perspectives for achieving carbon neutrality,” The Innovation, vol. 2, no. 4, p. 100180, Nov. 2021, doi: 10.1016/J.XINN.2021.100180.
[3] Architecture 2030, “Why The Building Sector? – Architecture 2030,” 2018. https://architecture2030.org/why-the-building-sector/ (accessed Sep. 25, 2022).
[4] N. Llantoy, M. Chàfer, and L. F. Cabeza, “A comparative life cycle assessment (LCA) of different insulation materials for buildings in the continental Mediterranean climate,” Energy Build, vol. 225, p. 110323, Oct. 2020, doi: 10.1016/J.ENBUILD.2020.110323.
[5] J. Zuo, B. Read, S. Pullen, and Q. Shi, “Achieving carbon neutrality in commercial building developments – Perceptions of the construction industry,” Habitat Int, vol. 36, no. 2, pp. 278–286, Apr. 2012, doi: 10.1016/J.HABITATINT.2011.10.010.
[6] SEI, “Top 10 Things Every Structural Engineer Should Know about Embodied Carbon – SE2050,” 2020. https://se2050.org/resources-overview/embodied-carbon/top-10-things-every-structural-engineer-should-know-about-embodied-carbon/ (accessed Sep. 24, 2022).
[7] rps, “Embodied carbon: What it is and how to tackle it | RPS,” 2022. https://www.rpsgroup.com/services/environment/sustainability-and-climate-resilience/expertise/what-is-embodied-carbon/ (accessed Sep. 24, 2022).
[8] Stephen, “Part Z Building Regs amendment would cap whole life carbon on newbuilds from 2027 | RIBAJ,” Riba Journal, Jul. 2021, Accessed: Sep. 24, 2022. [Online]. Available: https://www.ribaj.com/products/part-z-embodied-carbon-building-regulations-fcbs-whole-life-carbon-network
[9] J. Vickers, J. Chapa, S. Warmerdam, S. Qian, S. Mitchell, and N. Sullivan, “Title: Embodied Carbon and Embodied Energy in Australia’s Buildings,” Green Building Coucil Australia, Jul. 2021.
[10] T. Opher et al., “Life cycle GHG assessment of a building restoration: Case study of a heritage industrial building in Toronto, Canada,” J Clean Prod, vol. 279, p. 123819, Jan. 2021, doi: 10.1016/J.JCLEPRO.2020.123819.
[11] C. Piccardo, A. Dodoo, and L. Gustavsson, “Retrofitting a building to passive house level: A life cycle carbon balance,” Energy Build, vol. 223, p. 110135, Sep. 2020, doi: 10.1016/J.ENBUILD.2020.110135.
[12] N. Llantoy, M. Chàfer, and L. F. Cabeza, “A comparative life cycle assessment (LCA) of different insulation materials for buildings in the continental Mediterranean climate,” Energy Build, vol. 225, p. 110323, Oct. 2020, doi: 10.1016/J.ENBUILD.2020.110323.